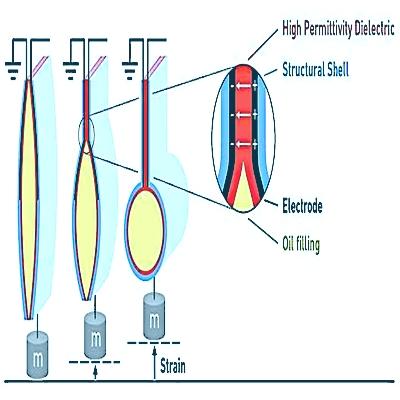
Artificial Robot Muscles Function Like Biological Muscles
A research team at ETH Zurich have just created artificial robot muscles to allow them to move. This is a significant improvement over previous technologies. It has applications where robots need to be soft or where more sensitivity is needed. Soft robots can interface with their surroundings in a totally different way, to soften blows like human arms and legs, or hold fragile objects without damage. Soft systems can store energy well, reducing power consumption.
They way these artificial muscles function is based on biological muscles. Artificial muscles contract in response to an electrical impulse like our muscles do. The artificial muscles, instead of being composed of cells and fibers, use a pouch filled with oil or sometimes other liquids.
The the shell of the pouch is partially covered in electrodes. When these electrodes receive electricity, they are drwan together and squeeze the liquid into the rest of the pouch, which flexes and is then able to lift a weight. A pouch is similar to a bundle of muscle fibers. A few of these can be connected together to form a complete "actuator", simply known as an artificial muscle.
Obstacles Overcome
Many attempts at creating artificial muscles have been tried, but electrostatic actuators only worked with extremely high voltages of 6,000-10,000 volts. This meant that the muscles had to be connected to large, heavy voltage amplifiers. Also, they couldn't work in water and posed some danger to people.
A new design has now been created by Robert Katzschmann, a robotics professor at ETH Zurich, working with Stephan-Daniel Gravert, Elia Varini and further colleagues. They have published their version of an artificial muscle that offers several advantages in Science Advances. Gravert, Katzschmann's lab assistant, has developed a shell for the pouch. The researchers call these new artificial muscles HALVE actuators, an acronym for "hydraulically amplified low-voltage electrostatic." This new design allowed the researchers to reduce the required voltage. One example is an 11-centimeter-tall gripper with two fingers. Each finger is moved by three pouches of the HALVE actuator connected in series. The small battery-operated power supply provides the robot with 900 volts.
Source: TechXplore
